内螺纹焊接铜管的生产工艺
来源:
捷邦换热 日期:2021-08-30
热交换器的换热性能,能够有效提升空调等制冷设备的传热效率。近年来,空调制冷行业开始普遍使用内螺纹铜管,但国内目前所使用的内螺纹铜管直径太小,施工人员对焊接标准和技术很难把握,内螺纹铜管的焊接问题成为急需解决的问题。
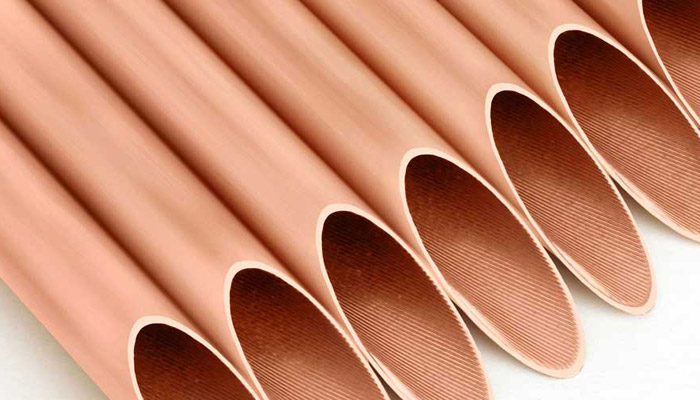
焊接管的生产工艺流程
制冷设备所采用的内螺纹铜管,主要原料为TP2紫铜带。内螺纹焊接管的生产工艺流程如下:1. 需要在铜带的表面轧制螺纹,在压螺纹工序过程中,需要注意的是压纹辊要根据螺纹的形状选择适宜的数量;
2. 在经过多次压辊后,铜带便逐渐成型,从而形成圆形后高频焊;
3. 运转铜带,焊接铜带的头部和尾部;
4. 当焊接完毕后,要用刀将螺纹管表面的毛刺刮掉;同时,为了保证焊接管的尺寸足够标准,还需要运用定径辊测量螺纹内管的外直径,如果其符合椭圆度公差要求,便可以进入层绕工序;
5. 在此工序结束后,便进入最后的退火工序,在该工序中,可以使用的工具为罩式炉和水平连续炉;
6. 退火完毕,直接进行包装,便可完成整个内螺纹焊接管的生产流程。
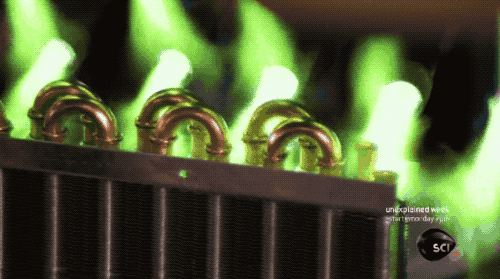
焊接管相较无缝管的优势焊接管的内壁清洁度要高于无缝管,原因就是焊接管会自动清扫自身内壁清洁度,其清洁标准已达国家标准的1/10。一般的无缝管内壁生锈,需要通过涂抹有机油,保持运转的平滑性,不致于影响制冷设备的正常运转,但是焊接管就不需要如此。
焊接管没有漏点,主要体现在生产过程和高速焊接工艺中。合格的焊接管材会直接进入生产环节,所使用的生产设备以及工具可以保持15天以上的正常生产稳定状态,而且所生产的焊接管不会存在任何缺陷。
除此之外,焊接管生产完毕后,会进入高速焊接工艺步骤,在此步骤中,设置了涡流探伤流程,从而切断不合格产品,以防其进下一步工序。
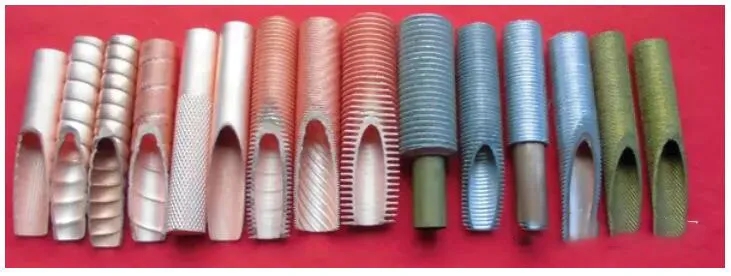
W 型焊接螺纹管主要是用于R407C 冷媒空调,当冷媒在管道内流动时,气液转换以及冷媒混合可以同步进行,缩减分层所带来的散热效率降低影响。除此之外,在使用过程中,还需要注意不同类型空调制冷剂的流动速度,如果W 型螺旋管已不适用于现有流动速度,那么,还可以将多V 型螺旋管添加其中。
交叉型焊接螺纹管,经常被使用在R410A 冷媒空调中,由于R410A 媒超强的蒸发压力弥补了交叉型螺纹压降损耗。因此当冷媒以较高的流动速度在管理运行时,其运行表面积已经远远超过W 螺纹管以及单旋管面积,因此,其散热效率也得到了同步的扩增。
螺纹铜管所应用的高频焊接工艺高频焊接的主要原理为:
首先,需要将所有电流汇集在待焊区域,然后进行加热,激发高频电流当中的集肤效应以及邻近效应,从而能够在最短的时间内完成加热工作,借助挤压棍,完成高频焊接流程。一般来说高频焊接主要包含两种不同的焊接方式:一是接触高频焊接,二是感应高频焊接。
接触高频焊接原理为:将高频焊接电流输入触头和管胚焊边缘区域,以此完成焊接工作。但是这种焊接方式,会极大地消耗电极触头,引发管坯变形,进而影响焊接质量;
感应高频焊接原理为:借助高频电流当中的肌肤效应和邻近效应,快速加热感应圈内温度,从而能够使穿过感应圈的待焊管胚,在高温的作用下,完成焊接流程。
目前,国内普遍使用感应高频焊接方式,这种焊接方式普遍被用来焊接直径小、内壁薄的有色金属管件。其不仅具有稳定的焊接过程,焊接质量优越,不需要消耗触点材料,同时调节起来也更加的容易。
感应高频焊接工艺(1)压纹。
压纹机不同的分组,可以完成不同的压纹过程。一般会分为两组,上轧辊主要负责加工螺纹的沟槽以及刻痕,而下轧辊所运用的结构为平面结构。两组轧辊会在带料表面压制组合沟槽。一般单旋螺纹只需要一组轧辊,便可以完成压纹过程。为了保证螺纹加工工作顺利进行,我们需要从以下几个方面入手:一是轧辊间隙和平行度。轧辊间隙的大小会决定焊接边厚度,进而最终导致不稳定焊接质量状况发生。轧辊间隙的调整需要足够的细致耐心,满足清晰、饱满的螺旋齿形要求,才能够保障螺纹尺寸符合生产标准;其次,轧辊的平行度调节,需要有效的控制设备安装轴。
二是关于提升焊接平稳度以及管材清洁度的要求。首先,轧制速度需要提升至200米/ 分钟,保持均匀的管材底壁厚度;其次,将没有轧制螺纹的边缘厚度与铜带底壁的厚度,两者之间的厚度差值保持在0.01 毫米以内;除此之外,轧制后的铜带表面应当螺纹清晰,为了防止产生波浪变形,可以在距铜带一毫米区域内压一条纵向平行的凸筋。
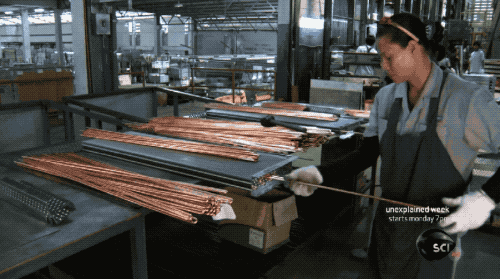
(2)圆管成型。
铜管的尺寸直接取决于铜管最终的成型状态。铜管焊接成型的流程为:运用胀扩杆撑开内螺纹铜管,然后将连接管插入螺纹铜管内,增大散热片和管壁的接触面积,从而进行焊接工作。除此之外,当铜管成型后,还需要根据实际应用,在保留铜管原有尺寸以及焊接平行对齐、焊接挤压余量充足的前提下做相应调整。普通的平片材料逐渐转变为圆管的实施过程为:首先,可以运用导向装置,将材料运输至成型机组,在保证材料变形中心对称的基础上,使材料能够借助轧辊与材料间的摩擦力,保持相同变形量前进,在经过不同组的轧辊后,从而形成圆管毛坯。
高频焊接间隙配合问题及解决方法(1)问题
第一,产晶尺寸最终取决于铜管原始尺寸。整径的范围过大或过小,都会直接影响焊管微观组织。除此之外,圆管成型原尺寸过小以及过大,会引发焊管变大以及焊缝对接边挤压量过少问题。与此同时,尺寸过大,会导致毛坯定型材料尺寸被拉宽,降低管壁厚度。第二,成型辊间距过小,分别会对材料毛坯、材料截面应力以及内螺纹铜管造成不同的影响。站在材料毛坯的角度,间隙过小会增大毛坯的变形量,导致焊接接近角呈现A 型;而从材料截面应力方面来讲,应力会呈现不均匀分布状态,在焊接完成后,必然会引发变形问题;而对于内螺纹铜管来说,其会削减压制成型螺纹高度,螺纹的形状受其影响会被改变。第三,还会引发材料的变形量呈现不均衡分布状态。材料会出现起皱现象,褶皱区域分布在材料的两边,并且褶皱处有明显的开裂以及焊缝缺陷。
(2)间隙问题解决方法
调整轧辊的间隙,我们可以采取以下几点方法:首先,我们需要以标尺上的刻度为依据,在确定轧辊的初始位置后,按照标准刻度,测量不同组轧辊之间的间隙;按照测量距离调整好后,可以将材料送到成型轮组中,观察材料边缘状态,从而能够适时地调整轧辊间隙大小;接下来进入焊接阶段,启动焊接设备,观察待焊接边的对接状况以及焊接过程是否稳定;焊接完毕后,分析焊缝是否达到标准。
(3)导向与焊接挤压。
导向与焊接挤压主要指的是,借助挤压轮所给的挤压力,将焊缝中的杂质以及融化金属等物质挤出,通过高温使固相金属紧密连接,以此完成焊接。需要注意的是,挤压力的大小会直接影响焊缝的牢固性以及焊接缺陷状况。例如,挤压力过大,会引发变形;过小,并不能挤出异物,从而导致焊接缺陷。调整挤压力大小,可以借助记压力设定值以及焊接过程,完善挤压轮间隙。市面上出现,一种陶瓷挤压轮,不仅解决了电能消耗问题,同时也提升了挤压轮的耐热性能,降低挤压轮冷却要求,减少焊接缺陷问题发生的概率。导向以及挤压轮之间的距离大小,可以通过对焊接区V 形角的调整进行改善。除此之外,调节导向轮,可以使焊缝位于毛坯上方,方便焊接工作进行。
综上所述,目前内螺纹焊接铜管工艺得到推广和普遍使用。该焊接管具有无缝管所无法比拟的优势,同时,借助高频焊接技术,增大铜管内部的表面积,从而扩张散热面积,有效提升制冷设备的散热性能。
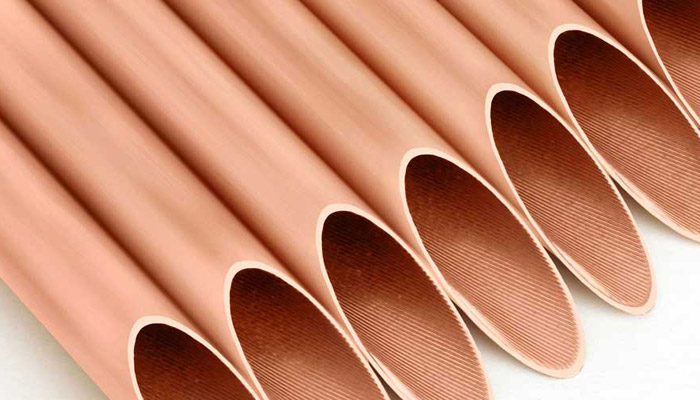
焊接管的生产工艺流程
制冷设备所采用的内螺纹铜管,主要原料为TP2紫铜带。内螺纹焊接管的生产工艺流程如下:
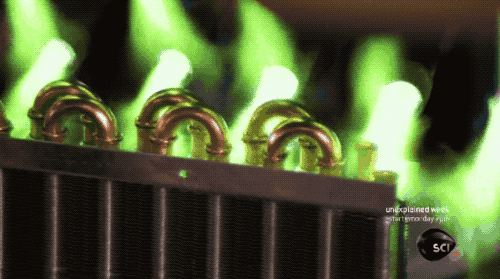
焊接管相较无缝管的优势
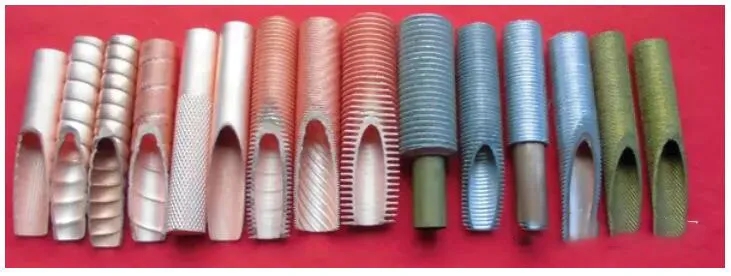
螺纹铜管所应用的高频焊接工艺
感应高频焊接工艺
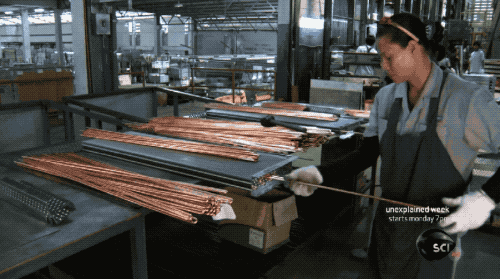
高频焊接间隙配合问题及解决方法
上一行业新闻:工业冷水机组的常见故障及解决办法?
下一行业新闻:换热器行业相关法律法规及政策汇总