壳管式换热器铜管缝隙腐蚀失效的分析

壳管式换热器(图1)由壳体、内螺纹换热铜管、折流板等部件组成。冷媒从1(冷媒进口)进入,流经6(高效换热铜管束)管内换热后从3(冷媒出口)流出,构成管程。水从2-2(进水口)进入5(壳体),在6(高效换热铜管束)外表面吸收热量被加热后从2(出水口)流出,构成壳程。正常情况管程、壳程之间密闭、只有热量交换不会发生流程材料泄漏。
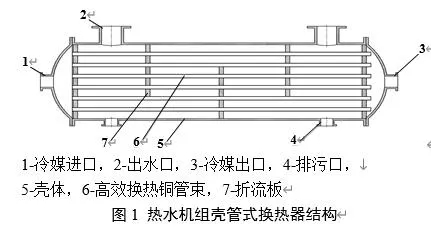
出现失效的多台商用空气能热水机壳管式换热器在售后工作3.5年~5年后,先后反馈机组报“低压保护”异常,维修人员排查确认为壳程流体(经处理的地下水)已泄漏进入管程(图2)。拆解发现折流板通孔处换热管束铜材有不同程度腐蚀、穿孔(图3铜管表面标红处),出现位置在系统过热、冷凝和过冷段未见明显集中,可排除系统工作环境的温度影响。

1.1 化学成分分析
对失效铜管取样进行化学成分分析,结果(质量分数)与GB/T 5231要求相符。
1.2 力学性能试验
在失效铜管上取样进行力学性能检测,结果与GB/T 17791要求相符。
1.3 断口金相(OM)检验
将失效铜管外观腐蚀深坑位做切面,并镶嵌、研磨、抛光,使用三氯化铁盐酸溶液对试样浸蚀,在金相显微镜下做断口金相检验。
铜管外壁呈不规则蚀坑(图4箭头),内侧齿形完好未见明显腐蚀,可以确定腐蚀方向为由外及内,及铜管表面或外侧壳层水中含有相关腐蚀介质。铜管基体为单相α铜(图5),呈完全退火态,晶粒平均直径约为0.025 mm,最大凹坑底部仍有小的腐蚀坑贯穿造成泄漏。
1.4 扫描电镜分析
将腐蚀泄漏铜管经超声波清洗后,置于PH ILIPS XL-30型扫描电子显微镜下观察,图6是泄漏处表面微观形态。
可见,泄漏处内表面存在腐蚀坑、裂纹、大量析出物,晶间优先腐蚀形成深邃裂纹。对内壁析出物(图6谱图1位置)进行X射线能谱分析(EDS),结果见图7。
结果分析:在Cu基材正常元素限基础上,Fe、Al、Mg、Si、Cl等元素偏高原因可能来自工作环境的地下水质,其中元素Fe、Cl的含量严重超出水源水质(见表1),为缝隙腐蚀反应析出的产物。
1.5 水质检测
依据GB 29044《供暧水质要求》标准与方法[9],对换热铜管工作环境的补充水水质进行取样、测试,检测结果如表1所示。
实验测得含铁量为18 mg/L,较GB 29044供暖水质要求(总铁≤1 mg/L)超过最大允许范围17倍。
文献指出,缝隙处于25~100 μm之间并且存在腐蚀介质,几乎所有的金属和合金都会发生缝隙腐蚀。本例壳管的铜管配入折流板通孔结构的设计间隙在0.2 mm,实测配合间隙为0.02 mm~0.30 mm之间,水样测试结果中Fe3+浓度18 mg/L(远超于水质标准要求的0.3 mg/L),同时存在一定量的Cl离子。组合形成的FeCl3通常用于工业上制印刷电路板时作为“腐蚀液”去除线路板上的多余铜,具有较强的腐蚀性,满足缝隙腐蚀产生条件。具体过程Fe3+作用下金属Cu在折流板缝隙或蚀孔中溶解,生成金属离子Cu2+,造成缝隙或蚀孔中的正电荷过量,使Cl-迁移到缝隙或蚀孔中以维持其溶液的电中性,缝隙或蚀孔内会存在高浓度的CuCl2,浓度梯度驱动CuCl2水解产生H+和Cl-,导致蚀孔进一步酸化、溶解(图8)、直至局部穿孔,腐蚀反应如下。
对壳管换热管束铜材(含折流板)进行DOE试验回归分析,试图寻找缝隙腐蚀速率、电位、电流与腐蚀介质浓度、时间之间的关系。
2.1 实验方法
取分析纯氯化铁与去离子水依次配置10 mg/L~140 mg/L不同浓度Fe3+(FeCl3)溶液,将换热铜管束(含折流板)置于其中。实验在热水机工作温度(90±5 ℃)条件下进行,每隔一段时间取出试样检查,并进行电化学参数实验,直至铜材表面出现明显腐蚀坑洞。
电化学参数实验采用经典的三电极体系,工作电极为铜电极,辅助电极为铂电极,参比电极为饱和甘汞电极,使用PARSTAT2273电化学测量系统进行极化曲线测试:极化曲线扫描速率为0.5 mV/s,在实验温度下测试相对于SCE的腐蚀电位。
2.2 TAFEL曲线分析
热铜管束(含折流板)在含不同浓度Fe3+溶液中浸泡216 h、432 h后铜材缝隙位的极化曲线如图9。
从曲线图可看出,换热铜管的腐蚀受电荷转移控制。采用PowerSuite软件对极化曲线进行电化学等效拟合(表2)。
随着氯化铁的增加,Cu的腐蚀电位、腐蚀电流发生正移或增大,添加50 mg/L时的腐蚀电位正移幅度约为137 mV、腐蚀电流增大约113%(相对于10 mg/L),之后腐蚀电位的移动幅度较小、腐蚀电流明显降低;金属在介质中的腐蚀电位与电流反映了金属表面状态和介质特性。添加氯化铁后腐蚀电流先增后减可能是由于Cu表面形成了某些暂态化合物或腐蚀产物阻碍腐蚀进一步进行。从表2中可以看出,腐蚀速率(腐蚀程度Icorr)随着氯化铁的增加呈现先增大后减小的趋势,腐蚀在较低浓度下存在腐蚀峰值。
2.3 腐蚀试验产物分析
将浸泡的换热铜管取出并立即采用去离子水清洗,发现隔板位置表面呈现紫铜砖红色和玫瑰红色(图11),金相分析发现腐蚀坑表面产生大量腐蚀产物,部分位置存在腐蚀产物覆盖隔离现象(图12)。
图13为腐蚀产物能谱图,铜表面腐蚀产物存在较高含量的C、O、Cu、Fe和Cl,其中O来自于腐蚀产物的吸附,表面该腐蚀产物部分位置较为疏松。较高含量的Fe表明氯化铁中的Fe3+参与了反应。对比图7售后腐蚀产物明显的Fe吸收峰,表明DOE试验存在与售后反应类似的腐蚀机理。
结论如下:
1)在10 mg/L~140 mg/L氯化铁水溶液中,Fe3+对Cu的缝隙腐蚀行为有重要影响,缝隙的浓度聚集作用在一定程度上促进了Cu缝隙腐蚀,高浓度时转化为均匀腐蚀。
2)铜的缝隙腐蚀速率随着Fe3+含量的增大呈现先增大后减少的趋势,腐蚀产物对腐蚀有一定的阻隔作用。
3)考虑到热水机壳管换热器使用环境,高效换热铜管的耐腐蚀性能优秀,但在评估地下水等非标水质对其腐蚀性影响时,应将铁离子含量控制考虑在内。